Industrial
Productivity Tools
|
Powerboss
a proven product!
Satisfied Powerboss customers from
thousands of installations around the world can attest to its ability to
save industry literally millions of pounds in energy and maintenance costs.
Independent reports from a variety of sources have endorsed both the quality
of engineering and economic viability of Powerboss. The following are just
a selection of the results from specific applications where careful monitoring
has taken place. |
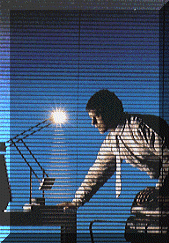
|
In May 1998, a test was carried
out by the giant French company - Aerospatiale. A 150 kW
Powerboss Plus was installed in the compressor room of the industrial plant
on a Siemens motor of nominal output 132KW. The installation, carried out
by a technician of Aerospatiale, provided a substantial annualised saving
of 30,572 kWh. In addition to the benefits of soft start.
|
|
At a Local Authority
site in Norway a 75kW Powerboss Plus has been installed on a Heat
Pump used to transfer heat from an Ice Rink to a nearby school. This efficient
heat transfer process, already saving the Authorities £100K per annum,
has been further enhanced by the installation of Powerboss. The calculated
payback for Powerboss is well within two years. |
At Volvo in Sweden
a 22KW Powerboss was installed in a line where the engine blocks are treated.
The motor operates under load 36% of the time and off load 64% of the time.
The metered energy savings of active power were 9% under load and 28% when
idling. Reactive power savings were 25% and 45% respectively.
Payback was calculated at 298
days.
|
Dillons,
a well respected retailer in the UK has over 700 shops throughout the group.
In 1992 they carried out an evaluation test in conjunction with an accredited
group of independent energy consultants, into the use and efficacy of the
single phase Powerboss on their refrigeration equipment. Initially one
shop was installed and after attractive energy savings were metered on
each unit, a pilot was carried out on a further ten shops enabling electricity
bills to be compared with previous periods. Following a successful installation
a roll-out programme was agreed resulting in over 4,000 units having
now been installed on equipment throughout the group. |
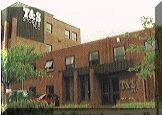
|
The much covetedDet Norske
Veritas approval has been awarded toPowerboss (with
limitations as to size and application) for installation on Ships and other
offshore installations. The evaluation also confirmed that the reduction
in electricity, which Powerboss undoubtedly makes, is translated into a
reduction in the amount of fuel consumed by the vessel, thereby extending
the time before refuelling.
|
|
At
one of the largest British Rail maintenance depots in the
South of England a 37kW Powerboss was installed on a motor used to drive
an air compressor. The site engineer metered the installation both before
and after the installation and reported a 21% saving in electricity. |
In
Norway, a large Municipal pump was causing considerable electrical
problems for a nearby factory. Despite having been fitted with a variable
Speed Drive, there was still very high starting currents causing transient
spikes and a drop in power in the immediate area – which resulted in computers
and electronic control equipment tripping out. All previous attempts had
failed to rectify the problem. However, following the installation of Powerboss,
the problem was eliminated and a permanent solution was provided. |
An
aircraft
manufacturing plant, employing over 4000 motors in its factories,
ran extensive tests on Powerboss. A wide variety of applications, including
vacuum pumps, sheet bending and cutting machines, lathes, horizontal boring
machines, and universal milling machines, were installed with Powerboss
and carefully monitored with excellent results. Savings, in kW hour, on
a wide range of motors averaged a staggering 38.4%. Following these
successful results an installation programme was agreed resulting in almost
1000
Powerboss having now been employed on one site. |
|
The
large American Company Contico installed and monitored a
Powerboss at a site in the UK. The unit was installed on a Granulator used
for re-cycling waste from the injection moulding machines. The installation
was monitored via an energy analyser and the results confirmed by the local
Electricity Supply Company. The motor ran throughout the day and kW savings
of over 50% were achieved for most of this period.
A laboratory test was carried out
by
Edwards High Vacuum Ltd. (Part of the British Oxygen Group)
into the suitability of installing Powerboss on their vacuum pumps. In
summary this eleven page comprehensive report stated: "the tests clearly
indicate that the Powerboss single phase energy controller reduces the
energy consumption of a typical single phase vacuum pump by between thirty
and forty percent". |
|
Curver
Limberg, one of the largest companies in the Benelux countries,
have a Powerboss installation on on of their Injection Moulding Machines.
During the production cycle, which varies dependant on the products under
manufacture, the equipment spends a proportion of time either off or under
low load. Following the Powerboss installation the energy consumption was
metered carefully and a cost saving of circa 20-25% was being achieved. |
In
Norway a 400kW ‘Rockmill’ capable of crushing 65 tonnes of granite
in circa 5 minutes was suffering from excessive starting currents even
when unloaded. A Powerboss PSO 400 provided an effective soft start solution
with complete motor and system husbandry. It was further noticed that the
motor spent over 40 minutes in each hour of operation in either a low or
unloaded condition. During these periods Powerboss reduced the power
consumption from 181kW to 153kW. |
A
manufacturing company, with the UK as 40% of its market for their top of
the range wood burning stoves, has 102 Powerboss 3phase units controlling
motors in its foundry. With a very hot and dusty environment, and some
motors
starting up to 400 times per day, the company experienced a very high
incidence of breakdown and consequent long periods of down-time on its
production lines. Although there has been an average saving of 22% in energy,
they also claim that the greatest benefit is the dramatic improvement in
equipment reliability and an almost 80% reduction in maintenance costs
due to improved motor control. |
For many people massive increases
in energy costs have become an unpleasant fact of life. Powerboss is cutting
through all the expensive ways to save energy by providing a brilliant
new answer to conquer those big energy bills. |
Tests & Certification
Summary of Declaration of Conformity
EMC Directive - 89/336/EEC
Low Voltage Directive - 73/23/ECC
Harmonised Standards - BS EN-61010-1-1993,
BS EN-60204-1:1992, EN 50082-2, EN55022
Class A and EN60555 - 2/3.
All Powerboss units carry a CE certification
mark
UL & CSA approvals pending
|
Powerboss has undergone
and passed the most stringent tests, and an EC Certificate of Conformity
proscribed by the EU has been issued.
Further numerous tests have been
carried out by: Equipment Manufacturers, Universities, Engineering Test
Houses and private companies to verify savings and equipment performance.
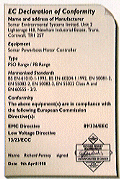
|
All IPT products are designed
to the highest possible standards and the manufacturing process is stringently
controlled for quality assurance
|
|